What is the Safety Factor of Insulation?
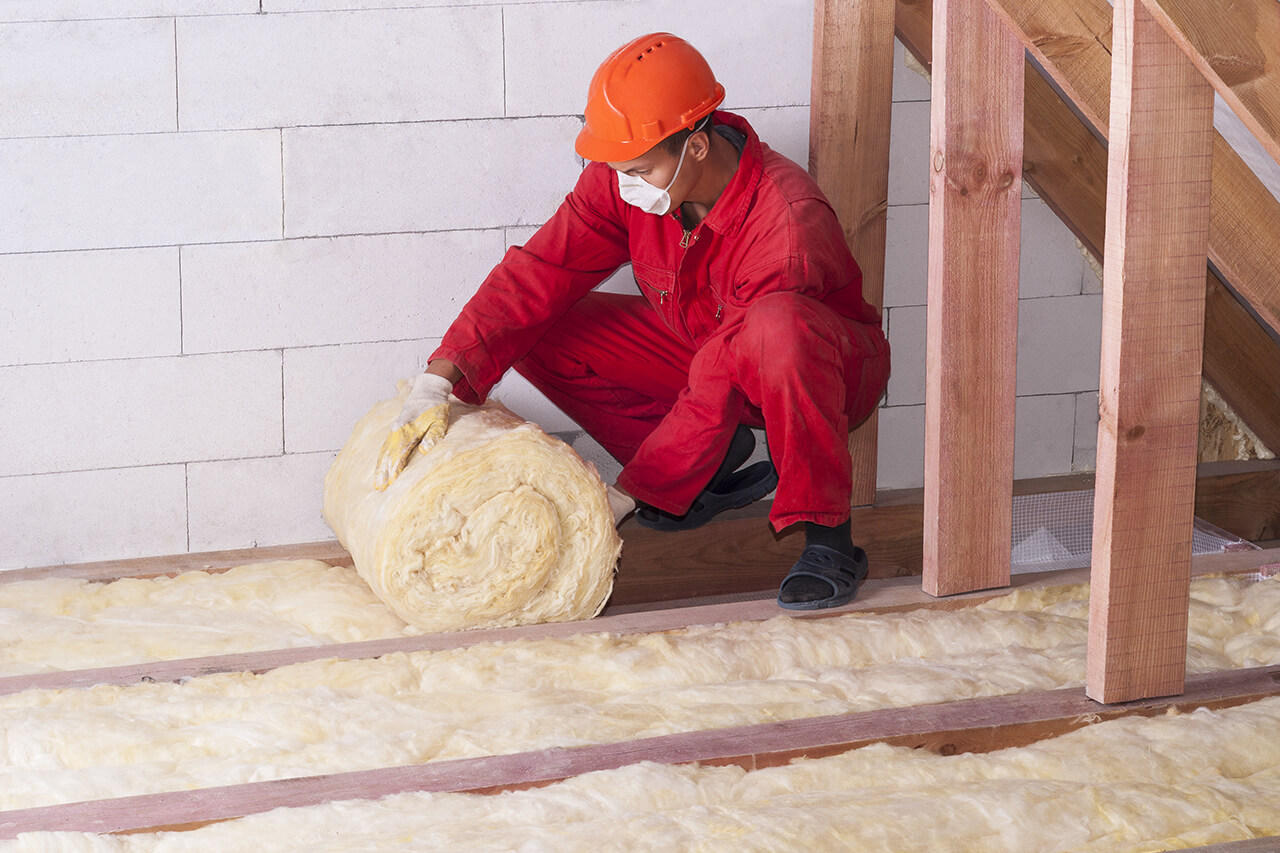
Insulation safety is a major concern for homeowners. They want to make sure their insulation is safe and that it will not cause any health problems.
In order to do this, they must understand how insulation is tested and what the safety factor is. This article will help explain these concepts.
What is the Safety Factor?
Insulators have to be designed to withstand both mechanical and electrical stresses. This includes the voltage that they must be capable of sustaining during line operations. Excessive stress can cause the insulator to break down either through flash-over or puncture. The latter involves the insulator becoming punctured by conductors or other metallic structures that are connected to it. The safety factor of an insulator is determined by the ratio of its puncture strength to its flash over voltage. For pin type insulators, this value is usually around 10.
When it comes to electrical safety, insulation needs to be able to withstand the maximum voltage that will be applied on a line. This is known as the peak voltage. It helps ensure that the insulator will not fail due to overloading during switching surges, faults or lightning strikes. This is why electric utilities design insulator lengths and clearances based on this value.
Besides electrical safety, there are also issues of health and environmental concerns when it comes to insulation. For example, some insulation is made of organic materials that can provide a food source for mold growth. This is why it’s important to make sure that you choose insulation that does not have any organic material in it. Fiberglass, mineral wool and spray foam insulation are inorganic materials that do not feed mold growth.
Another important consideration is the safety of insulation by Insulation Experts Sandpoint when it comes to fire resistance. This is especially crucial whhttps://selkirkenergysolutions.com/sandpoint-insulation-contractor/en it comes to commercial buildings and other large projects. If an insulator can’t resist fire, it could easily fail and become a hazard.
How is the Safety Factor Determined?
In order to determine which insulation materials are best for a specific application, you need to know more than just the insulating values of each material. You also need to understand how these values are calculated. This includes knowing about K, C, and R factors. These formulas will help you understand how the insulating values of various materials are determined and will give you the information you need to select the right type of insulation for your project.
The K factor is the rate at which thermal conductivity of a particular material is induced by temperature differences across its surface. The lower this value, the better the insulation’s ability to insulate. This measurement is made by testing a sample of the insulation material at different temperatures. A higher K value indicates that the insulation is more likely to conduct heat.
During the testing process, the insulation is subjected to impulse and power frequency voltages. The resulting test results are used to calculate the rated insulation level of a particular material or assembly. The higher the rated insulation level, the more effective it is at resisting the electric stresses that may be applied to the material.
In addition to the electrical stress, the insulator must be able to withstand mechanical stresses such as vibration and shock. For this reason, the insulator is designed with specific lengths and clearances to structural parts. This helps prevent outages caused by contaminated line insulation that can occur during switching surges, faults, and lightning strikes.
The insulation is also tested for resistance to currents that flow through the insulator. These currents are typically measured in millions of ohms (MO). However, modern testers can measure resistance in gigaohms (1 GO = 1,000,000,000 ohms). The resulting values are used to calculate the insulation’s temperature rating or its ampere rating, which is used to help ensure that employees will not be exposed to dangerous levels of electricity while working on electrical systems.
In addition to testing the electrical resistance of insulation, it’s important to check the chemical content of any insulators. This is because some insulators contain chemicals such as formaldehyde that can be harmful to human health. Fortunately, there are now a number of insulation products available that are made from materials that are free from formaldehyde. These materials are often more expensive than conventional fiberglass, but they can help ensure that employees stay safe while working on electrical systems.
What is the Difference Between the Shear and Tensile Factors?
Insulation is required to withstand mechanical stresses as well as electrical ones. The latter can cause a breakdown of the material, shorting it and allowing current to flow through the insulation. This occurs by either flashover or puncture of the insulation. Insulators are designed to withstand the voltages that they may be exposed to during transmission and distribution of electricity. This includes the voltages associated with switching surges and other fault conditions as well as lightning strikes. It is also important that insulators can withstand the maximum transient over voltages that they may be subjected to during maintenance of electrical systems and repairs.
In addition to mechanical stresses, insulators must be able to withstand stress caused by shear and tensile forces. Both shear and tensile strength are critical properties of any material, and engineers are constantly pushing the limits of what can be accomplished with different materials in terms of both these strengths.
When a material undergoes shear or tensile stress, it experiences a strain that causes the material to deform and change shape. Tensile stress occurs when forces acting perpendicular to the surface of an object pull on that material, attempting to elongate it. Shear stress is when forces act parallel to the surface of a material, trying to displace one part of an object from another.
A good example of shear stress is when you try to cut a piece of paper with a pair of scissors. You will notice that the paper tends to bend in a way that is reminiscent of a banana peel. This is because the paper is experiencing shear stress.
Tensile strength is a key property that many people look for in their insulation materials. Unfortunately, a lot of insulation products on the market today do not have sufficient tensile strength to meet the demands of the industry. However, many companies are working hard to improve the tensile strength of their products. Some of these improvements include using specialized heat treatments such as quenching and tempering. This is done to manipulate the microstructure of the material, thereby increasing its tensile strength.
What is the Difference Between the Tensile and Shear Factors?
The difference between the tensile and shear factors is that a tensile stress is created when a deforming force is applied at right angles to a surface, while shear stresses are generated by forces acting parallel to the surface. This means that when you pull a rope apart, it is experiencing a tensile stress. However, when you cut a rope with scissors, it is experiencing shear stress. This is because shear stresses cause objects to be elongated, while tensile stresses cause them to be compressed.
Another important distinction is that the shear strength of a material is less than its tensile strength. This is because shear stresses are much shorter in duration than tensile stresses. The shear strength of a material can be determined by using a shear test, which is a simple mechanical test that measures the amount of strain placed on an object in shear mode. The shear test can be conducted on any object, including wires, cables, and pipes.
In order to ensure that insulators are able to withstand the necessary mechanical and electrical stress, it is essential to use them properly. The electrical stress that is put on insulators depends on the line voltage, and excess voltage may break down an insulator in either flash-over or puncture.
It is important to understand the differences between tensile and shear factors in order to determine how safe it is to use different types of insulation. For example, cellulose insulation is more susceptible to shear stress than fiberglass insulation. This is because cellulose insulation is composed of wood fibers, which are not as strong against shear stress. Fiberglass insulation, on the other hand, is made from fiberglass filaments, which are more resistant to shear stress than cellulose fibers.
In addition to understanding the difference between tensile and shear factors, it is also important to understand how shear strength is incorporated into models. Shear strength is a key parameter for modeling because it provides a more accurate representation of the actual physical properties of mineral materials. This is because shear strength provides information on how a mineral will behave under a particular loading condition, and it is directly correlated to the tensile and compressive strengths of the material. This makes shear strength an ideal candidate for calibration.
Insulation safety is a major concern for homeowners. They want to make sure their insulation is safe and that it will not cause any health problems. In order to do this, they must understand how insulation is tested and what the safety factor is. This article will help explain these concepts. What is the Safety…
Recent Posts
- Affordable Fencing Solutions: Fence Company Rochester NY Offers Insight on the Cheapest Fence Installations in Rochester, NY
- Affordable Fencing Solutions: Fence Company Rochester NY Offers Insight on the Cheapest Fence Installations in Rochester, NY
- Exploring the Drawbacks of Duct Cleaning: Insights from Air Vent Cleaning Charlotte
- Exploring the Drawbacks of Duct Cleaning: Insights from Air Vent Cleaning Charlotte
- Clearing the Dust: Duct Cleaning Louisville KY Shares Tips to Make Your Home Less Dusty